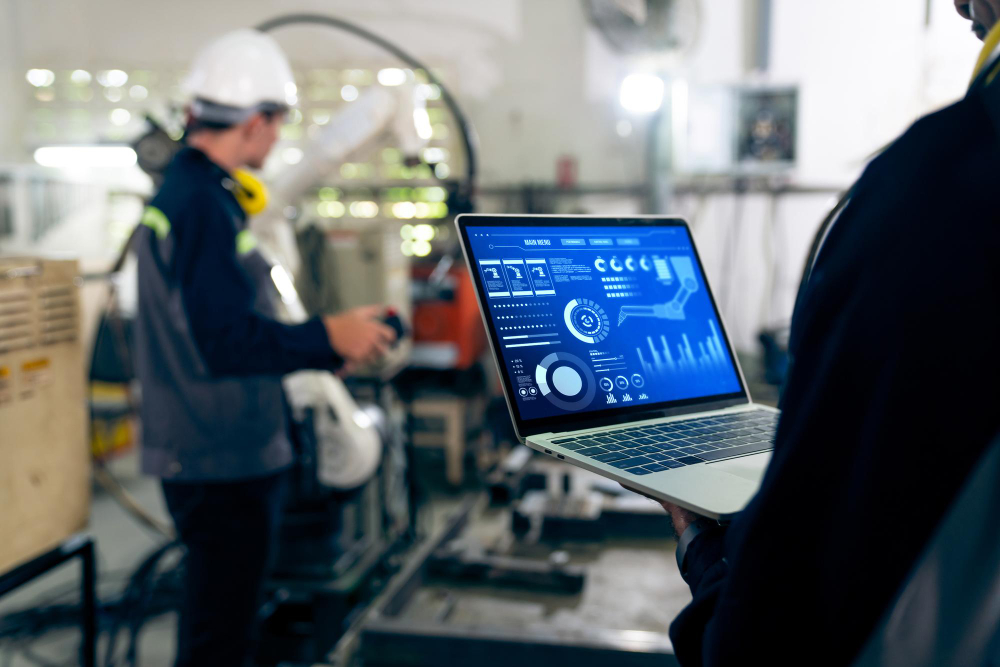
Indice
- Cos’è Industria 4.0? Definizione di Industria 4.0
- L’evoluzione di Industria 4.0: i processi industriali negli anni
- Le tecnologie che guidano Industria 4.0
- I vantaggi dell’Industria 4.0
- Hub e Competence Center
Cos’è l’Industria 4.0? Molti professionisti hanno sentito spesso fare riferimento a questo termine in ambiti quali la produzione, l’ingegneria e la produzione, ma cosa significa veramente?
In poche parole, Industria 4.0 è un termine utilizzato per definire l’ultima generazione del mondo “industriale”. Nel corso dei secoli, il modo in cui produciamo prodotti, produciamo soluzioni e in generale innoviamo si è evoluto drasticamente.
Dalla prima rivoluzione industriale, quando gli esseri umani hanno migliorato la meccanizzazione attraverso l’energia dell’acqua e del vapore, alle catene di montaggio della produzione di massa dell’Industria 2.0, abbiamo costantemente cercato modi per rendere la produzione più efficiente.
L’Industria 4.0 è la “quarta rivoluzione industriale”, un concetto che si basa sull’informatizzazione e la digitalizzazione introdotte nell’Industria 3.0. In questo panorama, i computer e le persone sono più profondamente connessi, consentendo l’uso dell’automazione, dell’intelligenza artificiale e dell’Internet delle cose.
Cos’è Industria 4.0? Definizione di Industria 4.0
L’Industria 4.0, o la quarta rivoluzione industriale, porta il lavoro iniziato a migliorare e digitalizzare i processi di produzione e produzione nell’Industria 3.0 al livello successivo. Laddove l’Industria 3.0 ha introdotto computer e macchine potenti nel processo di produzione, l’Industria 4.0 si concentra sulla connessione di questi dispositivi e consente loro di comunicare in modo più efficiente.
L’Industria 4.0 segna l’introduzione di processi intelligenti, automazione e sistemi connessi nel panorama industriale. Quando pienamente applicata, la tecnologia può supportare la creazione di “smart factories” e processi creativi autonomi.
Gli elementi dell’Industria 4.0 possono essere applicati a tutti i livelli del processo di produzione. Dal processo di produzione iniziale allo sviluppo del prodotto e persino alla gestione del ciclo di vita del prodotto. Alcuni produttori applicano persino i concetti di Industria 4.0 a risorse esterne come le catene di approvvigionamento, consentendo loro di anticipare meglio e gestire le interruzioni delle forniture.
L’evoluzione di Industria 4.0: i processi industriali negli anni
L’Industria 4.0 si è guadagnata il nome come la quarta grande rivoluzione nel panorama industriale. Secondo gli esperti, ci sono stati vari cambiamenti significativi nei processi di produzione nel corso degli anni. La prima rivoluzione industriale iniziò alla fine del 18 ° secolo, aprendo la strada alla produzione di massa tramite acqua e vapore. I prodotti finiti potrebbero essere prodotti da macchine piuttosto che a mano.
Nella seconda rivoluzione industriale, circa un secolo dopo, furono introdotte nuove catene di montaggio con energia a gas, elettrica e petrolio. Queste innovazioni furono rafforzate dall’introduzione di migliori capacità di comunicazione tramite telegrafi e telefoni. La terza rivoluzione industriale, iniziata a metà del 20° secolo, ha aggiunto telecomunicazioni avanzate, computer e analisi dei dati ai processi di produzione. I controllori di linguaggio programmabili hanno iniziato ad automatizzare determinati processi.
Ora siamo nella quarta rivoluzione industriale (Industria 4.0), caratterizzata da una maggiore automazione, dall’uso di macchine e da una maggiore attenzione ai dati. L’Industria 4.0 ha introdotto l’intelligenza artificiale, i flussi di lavoro intelligenti e l'”Internet of Things” nella produzione.
Le tecnologie che guidano Industria 4.0
Attualmente, l’Industria 4.0 è caratterizzata da una rapida evoluzione e trasformazione. Tuttavia, ci sono alcune tecnologie specifiche della quarta rivoluzione industriale che aiutano a separare il concetto da alcune precedenti innovazioni del settore, come ad esempio:
- Cloud computing: il cloud computing sta rapidamente diventando la pietra angolare di praticamente qualsiasi strategia Industry 4.0. Le tecnologie cloud consentono una facile integrazione di supply chain, ingegneria, produzione, vendite e assistenza. Inoltre, le tecnologie cloud consentono alle aziende industriali di raccogliere e utilizzare facilmente dati provenienti da vari ambiti.
- Edge computing: accanto al cloud computing, l’edge computing è cresciuto come parte cruciale di Industria 4.0. Le esigenze della produzione in tempo reale in un panorama manifatturiero innovativo completano alcuni processi di analisi laddove vengono creati i dati. L’edge aiuta anche le aziende a ridurre al minimo i rischi per la sicurezza.
- Internet of Things: IoT o Internet of Things consente una comunicazione rapida tra varie macchine sul piano di produzione. Le macchine sono dotate di sensori che consentono loro di connettersi con altri dispositivi ottimizzati per il Web tramite il cloud. Ciò consente una rapida raccolta di dati e una maggiore automazione.
- Machine learning e AI: l’introduzione di componenti avanzati di IA e machine learning consentono alle aziende manifatturiere di sfruttare appieno le informazioni che generano durante tutto il processo industriale. I sistemi di intelligenza artificiale possono fornire informazioni sui processi aziendali e aiutare le aziende a rimanere un passo avanti rispetto ai potenziali problemi con i dispositivi. Questi strumenti consentono anche un’automazione più avanzata.
- Gemelli digitali: le trasformazioni digitali offerte dall’Industria 4.0 hanno permesso ai produttori di progettare gemelli digitali, che sono essenzialmente repliche virtuali di fabbriche, processi, macchine, linee di produzione e catene di approvvigionamento. I produttori possono utilizzare i gemelli digitali per scoprire nuove opportunità per migliorare la produttività e ridurre al minimo i tempi di fermo macchine.
- XR: un’aggiunta relativamente nuova al panorama dell’Industria 4.0 è la realtà estesa. Attraverso strumenti di realtà virtuale, aumentata e mista, le aziende possono semplificare l’innovazione, aumentare la creatività sul posto di lavoro e migliorare la collaborazione su scala globale. L’XR può anche consentire la produzione di nuovi prodotti a un ritmo più rapido.
I vantaggi dell’Industria 4.0
Industria 4.0 può offrire numerosi vantaggi alle organizzazioni che la implementano con successo. Con le tecnologie offerte dall’Industria 4.0, le aziende possono costruire sensori, monitorare i processi di produzione in tempo reale e ridurre al minimo i tempi di fermo imprevisti. È anche possibile raccogliere dati su scala significativa per aiutare a migliorare il processo decisionale e la crescita.
Le tecnologie Industry 4.0 possono migliorare la formazione, la collaborazione e la conformità dei dipendenti, riducendo non solo i problemi di sicurezza informatica, ma anche i rischi per la salute e la sicurezza. Questo processo può anche aiutare ad automatizzare le attività ripetitive, migliorando la velocità dei processi di produzione e consentendo ai nuovi prodotti di andare sul mercato ad un ritmo più veloce.
Le tecnologie Industry 4.0 come l’XR possono persino aiutare con la creazione di nuove tecnologie e prodotti a un ritmo sorprendente. In questo modo possono consentire ai creators di costruire nuovi concetti senza dover investire in risorse fisiche. Tuttavia, anche l’Industria 4.0 ha dovuto affrontare alcune sfide.
Nel corso degli anni, le aziende hanno faticato a trovare le competenze e il budget necessari per implementare le tecnologie Industry 4.0 aderendo agli standard di conformità e sicurezza informatica. La connettività tra i dispositivi può esporre le aziende a una serie di sfide per la sicurezza.
Tuttavia, con l’evoluzione, Industria 4.0, sta diventando sempre più sicura, versatile e accessibile. Oggi, quasi tutte le aziende industriali dispongono di una tecnologia digitale innovativa per aiutare a semplificare le operazioni.
Hub e Competence Center
Con il piano Industria 4.0 è stato avviato il percorso per la creazione dei Competence Center, gli otto centri di eccellenza per l’Industria 4.0. A febbraio 2019, a Torino, si è svolta la prima tappa del roadshow nazionale per fare una sintesi della strada perseguita e portare le prime testimonianze delle imprese che hanno investito nelle fabbriche connesse.
Gli otto Competence Center sparsi per l’Italia (Torino, Milano, Bologna, Genova, Padova, Pisa, Roma e Napoli) hanno coinvolto nei partenariati circa 400 imprese e oltre 50 università.
I centri di competenza hanno il compito di svolgere attività di orientamento e formazione alle imprese, nonché di supporto nell’attuazione di progetti di innovazione, ricerca industriale e sviluppo sperimentale. Tutto questo finalizzato alla realizzazione di nuovi prodotti, processi o servizi (o al loro miglioramento) tramite tecnologie avanzate in ambito Industria 4.0.